Choosing a power supply for reliable operation in dirty environments
Monday, July 25, 2022
TDK-Lambda’s power supplies are frequently used in industrial applications and many times subjected to dirty environments; by this I mean dust, dirt and condensation.
Excessive amounts of dirt can cause premature failures and the power supply’s end user will often request failure analysis due to lost production. I have even seen returned products full of coal dust, sawdust and even copious amounts of metallic star shaped glitz from a postal sorting application!
Figure 1: Returned power supply.
One method of determining if a product is suitable for an application is to refer to its Pollution Degree (PD) classification (Table 1). This can be found on the safety certification reports such as IEC 60601-1, IEC 62368-1 and IEC 61010-1, to name the most popular.
Pollution Degree 1 |
Pollution Degree 2 |
Pollution Degree 3 |
Pollution Degree 4 |
No pollution or only dry, nonconductive pollution occurs |
Non-conductive pollution that with occasional condensation could become temporarily conductive |
Conductive pollution is to be expected, with or without condensation |
Persistent conductivity, rain or even snow is the norm |
Sealed enclosures or Semi-Feb clean rooms |
Office environments, laboratories and test equipment |
Industrial & farming applications, food preparation and unheated or boiler rooms |
Outdoor equipment |
Table 1: Classification and examples of Pollution Degree Categories
One problem facing designers is finding a suitable power supply that is classified as PD-3. To meet that rating may necessitate adding additional spacing between the copper traces on the pcb and between components. This can increase the size and raise the cost of the product thus making it non-competitive against mainstream products; this then reduces the number of products available on the market. As the end system may not mandate that rating, designers often opt to select a PD-2 classified power supply. There are several ways to maintain product reliability as outlined below.
Printed circuit board coating (conformal coating) can provide protection against conductive pollution and occasional condensation. The food processing industry often specifies power supply board coating for power supplies for example. The major customer concerns are which type of coating is being used, how is it applied to the boards and how is it inspected afterwards. Varnish applied manually with a brush is more likely to have repeatability issues. Masking will be required for capacitor vents, and connectors. The performance of magnetic components may be impacted as the coating can change the core characteristics during the curing period. Fortunately, some manufacturers offer this as standard or as an option, like the TDK-Lambda HWS/HD series of AC-DC power supplies (Figure 2).
Figure 2: TDK-Lambda HWS Series of AC-DC power supplies
Convection or conduction cooled power supplies do not require forced air cooling to operate, either by an internal fan or system air. Any internal heat losses are dispersed naturally or conducted into the system chassis or cold plate. The use of this type of design reduces the product’s exposure to airborne contaminants being drawn in, building up over time, and later causing a failure. The TDK-Lambda CUS-M series has several models available at different power levels.
A sealed enclosure is another option for a conduction cooled power supply. The PFH500F AC-DC power module (Figure 3) is often used in outdoor equipment for LED displays. When using this type of product, ensure that the enclosure is of a sufficient size to allow natural convection airflow to circulate within.
Figure 3: PFH500 AC-DC conduction cooled power module
Power supplies with an internal low or variable speed fan are less likely to draw in dirt or dust than a power supply with a high-speed fan or multiple fans. This is due to the lower volume of air passing through the product. The QM modular series has low airflow, variable speed fans. This is primarily for minimizing acoustic noise levels but will still reduce the influx of dirt! Figure 4.
Figure 4: QM modular series AC-DC power supplies with low airflow
Ensure that the power supply exhausts its hot air out of the system enclosure. Power supply manufacturers may provide “reverse air” options. This can involve additional derating with temperature, so read the instruction manual thoroughly. Utilizing baffles in the system enclosure can direct airflow containing dirt away from the power supply.
Rack mounted power supplies like the GENESYS+™ programmable products have optional snap-on dust filters.
Figure 5: GENESYS+™ programmable power supply and the dust filter option (lower photograph)
Lastly replacement during scheduled maintenance. A surprisingly large number of manufacturers treat lower wattage power supplies as a disposable item, particularly when it is being used in a harsh temperature environment. At elevated temperatures, components like electrolytic capacitors have dramatically reduced life - for every 10oC rise in temperature the capacitor life is cut in half. Considering the cost of a service call, this may be a cost-effective option.
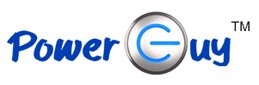