Using non-isolated DC-DC converters to simplify your power requirements for a new project
Wednesday, July 2, 2025
Introduction
The initial planning of a system or a machine’s power architecture can be a complex task as there can be a number of ways to derive the required voltages and currents. Cost, efficiency, size and certainly a consideration for system expansion are factors that should be considered. Many engineers create a “power budget” to determine what is needed to achieve this.
AC-DC power supply types
There are many types of AC-DC power supplies available, ranging from fixed, single output products to modular types with multiple outputs. Each type has their advantages and their disadvantages. For example, Industrial AC-DC DIN Rail mountable 24V power supplies continue to gain popularity due to their low cost, convection cooling and a number of back-up power accessories. As they do not rely on forced air cooling, they are larger than an open frame product.
Isolated DC-DC converters
To provide the low voltage, low power outputs required for control boards and other circuitry, traditionally isolated board mount DC-DC converters have been used, drawing their input power from the system power supply. These typically range from 0.5W to around 60W, have either single or dual outputs, and rely on either convection or conduction cooling. Although trim pins for output voltage adjustment are provided on single output converters, their range is quite narrow, in the order of -10% to +10%.
If higher power isolated DC-DC converters are required, 50 to ~900W industry-standard “brick” modules tend to be used. These are referred to in the industry as sixteenth, eighth, quarter, half, and full “bricks”. These rely on system airflow and an optional heatsink. Like board mount converters, these also have minimal output adjustment.
Non-isolated DC-DC converters
At first glance, it would seem that using a non-isolated DC-DC converter in a system would be an infringement of the primary -secondary safety barrier. This is not the case as the system AC-DC power supply is designed to meet the appropriate safety standards and will have sufficient creepage and clearance to meet the demands of the international standards including IEC62368, IEC61010 and IEC60601.
The most widely used types of these converters are buck, boost and buck-boost DC-DC converters.
A buck converter reduces the voltage and the output voltage is lower than the input voltage. See Figure 1.
Figure 1: Buck converter
When transistor S is turned on, energy is stored in inductor L as the current flows to the load and Capacitor C is charged. When S is off, the energy stored in L is released and current flows into the load and circulates via diode D. Capacitor C also provides energy to the load. This is repeated at high frequencies, greater than 100,000 times a second. The length of the time S is turned on defines the output voltage.
A boost converter increases the output voltage higher than the input voltage. See Figure 2
Figure 2: Boost converter
When transistor S is turned on, current flows through inductor L, through transistor S back to the input. During this period energy is stored in the inductor. When transistor S is off, the inductor acts a voltage source in series with the input voltage. The inductor’s stored energy is circulated through diode D to the load. This charges capacitor C to a higher level than the input voltage. Again, the length of the time S is turned on defines the output voltage.
A buck-boost converter is a combination of a buck and boost converter. The output voltage can be higher or lower than the input voltage. See Figure 3.
Figure 3: Buck-boost converter
As you can see the circuit is more complicated and has more components, S2, L, and D2 is the boost converter and S1, L and D1 the buck section.
A non-isolated DC-DC converter is inherently simpler and lower cost than an isolated converter. There is no isolation transformer and no optocoupler, resulting in a more compact product and lower heat losses and overall efficiency. When the load is subject to sudden changes, a non-isolated circuit has a better transient response with faster recovery.
Battery powered equipment
Automated guided vehicles (AGV), industrial mobile robots (IMR), drones, commercial off-the-shelf (COTS), industrial, test, measurement and medical applications are now increasingly relying on batteries to provide their source of power.
This introduces new challenges to the designer including battery life, physical space and weight limitations, minimal system cooling and increasingly higher costs.
Comparing the 12V output 1x1” TDK-Lambda 30W rated 1x1” CCG to the i1C, where both can accept a 9 to 36Vdc input, we can see a very large difference in performance.
Model |
Isolation |
Efficiency |
Output Power |
Output range |
CCG30 |
Isolated |
87% |
30W |
10.8 – 13.2V |
i1C |
None |
98% |
200W |
9.6 – 28V |
Figure 4: CCG30
Figure 5: i1C
In addition to its higher power density and efficiency, the non-isolated module features a wider adjustable output range streamlining inventory management by enabling a single part number to support multiple output voltages and be used across various products.
Many of the TDK-Lambda non-isolated models offer a choice of cooling formats. These include open frame, cold-plate mount (for sealed enclosures using thermal gap filler pads and threaded mounting screws) and a heatsink for forced air cooling.
Summary
When selecting a supplier of non-isolated DC-DC converters, chose a manufacturer that has a large range of products to best optimize your system performance.
If the product is powering a drone, weight will probably be of high importance and may require an open frame or baseplate model, rather than a version with a heatsink.
A customer selecting an industrial mobile robot (IMR) operating in a warehouse will require an extended battery run-time, to maximize its operation and minimize its recharge time.
For applications requiring remote adjustment of the output may consider a model with a digital interface to reduce the charging time of the on-board battery.
It is anticipated that the output power of non-isolated converters will continue to rise and provide even more features. Before starting a new program, contact your local field application engineer for free advice.
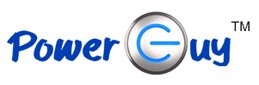