Applications and use of EMI Filters for Industrial and Medical Applications
Tuesday, October 1, 2024
In today's technologically driven world, electronics play a pivotal role in our daily lives. From smartphones to industrial machinery, the abundance of electronic devices has led to an increased need for effective Electromagnetic Interference (EMI) and Electromagnetic Compatibility (EMC) filtering. These filters ensure that electronic devices function harmoniously without causing or being affected by unwanted electromagnetic emissions. By exploring fundamental EMI/EMC concepts, regulatory considerations, and practical applications, we can provide a comprehensive understanding of the importance of EMI filtering in our increasingly electronic world, along with some guidance for engineers on selecting the right filters for their specific needs.
UNDERSTANDING EMI AND EMC
Emissions are electromagnetic disturbances generated by electronic devices that can interfere with the operation of other devices. These disturbances can be caused by numerous factors. The following are examples of common sources of electromagnetic interference.
Switching Transients: Common in power supplies and digital circuits, switching transients occur when currents or voltages change abruptly. These rapid changes can generate high-frequency harmonics, leading to electromagnetic emissions.
Clock Signals: In digital electronics, clock signals synchronize the operation of different components. The fast rise and fall times of these signals can produce significant harmonic content, contributing to emissions.
Functional Electromagnetic Fields: Motors, transformers, and other inductive components generate electromagnetic fields as part of their normal operation. When these fields fluctuate, they can induce currents in nearby conductive paths.
Signal Harmonics: Non-linear elements in a circuit, such as diodes and transistors, can distort signals, creating harmonics that extend into the radio frequency range. These harmonics can radiate or be conducted away from the device, causing interference.
Understanding EMI, EMS and EMC:
EMI is Electromagnetic Interference and refers to the disruptive electromagnetic energy emitted by a device. EMS is Electromagnetic Susceptibility is the ability of a device to withstand external electromagnetic disturbances without degradation in performance, while EMC is Electromagnetic Compatibility and the overall compliance to EMI and EMS requirements, EMI + EMS = EMC.
Emissions vs. Immunity: Emissions are the electromagnetic energy generated by a device, which can potentially interfere with other devices. Immunity, on the other hand, is the ability of a device to withstand external electromagnetic disturbances without degradation in performance.
Radiated vs. Conducted: Electromagnetic Emissions can be either radiated, meaning they propagate through air or space, or conducted, meaning they travel along conductive materials like wires or cables. Each type of emission requires specific mitigation strategies to prevent interference.
REGULATORY CONSIDERATIONS
The proliferation of electronic devices in modern society has necessitated stringent legislation to ensure their safe and harmonious operation. This legislation mandates compliance with specific Electromagnetic Interference (EMI) and Electromagnetic Compatibility (EMC) standards, applicable to manufacturers and designers of electronic equipment. Understanding these regulatory implications is crucial, as non-compliance can lead to legal repercussions, product recalls, and damage to a company's reputation.
Regulatory requirements for EMC compliance can vary by region, making it essential for manufacturers to understand and adhere to the standards specific to each market in which they operate. For instance, products sold in the European Union must comply with the EMC Directive (2014/30/EU), while those in the United States must meet FCC regulations.
Many regulations require that manufacturers certify their devices against the applicable regional requirements through a recognized or authorized third party evaluator. Even in regions where supplier self-declarations are technically permissible, it is usually wise to seek third party evaluation as a demonstration of due diligence.
APPLICATIONS FOR EMI FILTERS
Stand-alone EMI filters play a vital role in enhancing the performance and reliability of complex systems across industrial and medical sectors. Let's take a closer look at some common applications in these spaces.
1.Power Supplies and Power Systems:
In both industrial and medical environments, power supplies must be able to provide consistent, stable electrical energy. EMI filters are needed to prevent grid disturbances from propagating to downstream equipment that may not tolerate it, and at the same time ensure that high frequency energy produced by the switch mode power conversion does not propagate upstream out onto the grid where it could potentially disrupt other off-line equipment nearby. EMI filters in power systems are crucial for eliminating noise that can cause disruptions in sensitive equipment, leading to errors or failures. For instance, in precision manufacturing, even minor power quality issues can result in significant production defects.
2. Rotating Machines
Much of the world’s total electrical load is comprised of rotating machines. Pumps and motors are key components in most of our higher powered devices such as house-hold appliances like air conditioners, refrigerators and laundry machines, or industrial devices like elevators, escalators, automated production machines or laboratory instruments like centrifuges. EMI filters contribute to device longevity by preventing premature wear and tear caused by electrical noise. In applications like CNC machines or robotic arms, this translates to smoother operation and reduced maintenance costs. Motors and pumps are also notorious for inducing electrical noise in nearby equipment. This noise is typically generated by the switching actions of the motor's control circuits, such as those found in variable frequency drives (VFDs), and by the commutation process in the case of brushed motors. The rapid switching of currents and voltages can produce electromagnetic interference (EMI) in the form of both conducted and radiated emissions.
- Transmitting Devices
In industrial communications equipment, EMI filters are pivotal in preserving signal integrity. They ensure that data transmitted between sensors, PLCs, and control systems is accurate and free from corruption. This is particularly crucial in automated processes where real-time data exchange is essential for coordination and efficiency.
- Renewable Energy Systems
In renewable energy systems, power inverters and DC to DC converters play a key role integrating solar or wind power into the grid. Much like with power supplies, the switch mode power conversion networks within these devices can generate strong electromagnetic fields that can manifest as both radiated and conducted emissions. These fields are the result of the high speed switching action of transistors creating rapid voltage and/or current discontinuities which contain a wide spectrum of frequency components, including high-frequency harmonics, which can interfere with the operation of nearby electronic equipment.
- Industrial Machinery
EMI filters in industrial machinery contribute to overall system integrity. They help in ensuring that the electromagnetic noise generated by the machinery does not compromise the accuracy of control systems or sensor readings. This is critical in processes like precision machining or automated assembly, where even small errors can lead to significant quality issues.
- Medical Applications
The medical care environment introduces several unique risks and challenges with regard to Electromagnetic Interference (EMI) and Electromagnetic Compatibility (EMC) due to the critical nature of medical devices and the sensitivity of the patients.
The foremost concern in the medical care environment is patient safety. EMI can lead to malfunctions or inaccurate readings in medical devices, which can have dire consequences, such as incorrect diagnoses, inappropriate treatments, or even life-threatening situations. The care environment introduces a potential conflict between several devices that are both extremely noise-sensitive and extremely noisy. Many medical devices are highly sensitive to electromagnetic fields. For example, devices like pacemakers, defibrillators, and neurostimulators can be affected by EMI, potentially leading to incorrect operation or failure. However, hospitals and clinics often have a high density of electronic equipment, including MRI machines, X-ray machines, CT scanners, and various wireless communication devices capable of generating strong electromagnetic fields. This creates a complex environment, increasing the potential for EMI.
Manufacturers need to take additional precautions in the design of EMC filters for medical applications as the safety features of the filters themselves are also held to a higher standard. These filters must exhibit constructional features such as increased isolation levels and lower leakage currents.
Because of these risks, medical devices are subject to stringent regulatory standards for EMC to ensure their safe and effective operation. Compliance with these standards can be challenging, given the diverse range of devices and the dynamic nature of the medical care environment. The medical care environment is constantly evolving, with new technologies and devices being introduced regularly. This dynamic nature requires ongoing assessment and management of EMI and EMC risks to ensure the continued safety and effectiveness of medical devices. The selection of suitable EMI and EMC filters for these applications is paramount to product success.
FILTER SELECTION
Selecting the right EMI filter is a critical decision that hinges on understanding the specific needs of the application. The process starts with ensuring that the filter's current and voltage ratings are compatible with the device's operating conditions. It is noted that the steady state current rating is not the only current rating to consider. Often a filter must be able to withstand the systems full short circuit current rating (SCR) for a specified duration. The suppression levels, measured by the filter's insertion loss, should align with the required levels for effective noise mitigation. It is also important to consider the frequency range of the interference, as the filter must be capable of attenuating noise within this spectrum. The type of filter, whether it be common-mode, differential-mode, pi-filter, low pass, high pass or band pass all depends on the nature of the interference and the application.
The choice between different types of EMI filters, such as differential mode, common mode, or PI filters, depends on the nature of the noise source and the specific filtering requirements of the application. Differential mode filters are designed to attenuate noise that is present between the line and neutral conductors, typically generated by equipment high clock or processor speeds, or other fast-switching electronic components. Electromagnetic reflections in circuit conductors resulting from impedance mis-matches can also generate strong differential currents. On the other hand, common mode filters are used to address noise that is present between both the line and neutral conductors and ground. This type of noise is usually generated by electromagnetic interference from external sources, such as radio frequency interference or electromagnetic pulses, and can also be caused by ground loops, long cable runs, or imbalances in the electrical system. Switching transients in power conversion networks can introduce both differential mode and common mode noise.
PI filters, which consist of a series element (usually inductive) and two shunt elements (usually capacitive), are used when both differential and common mode noise need to be attenuated. They are effective in providing a broad range of filtering and are often used in applications where the noise environment is complex and contains both types of noise.
Once the exact type of filter and its necessary electrical characteristics have been established, one must consider the physical characteristics of the filter, such as size, mounting style, and terminal configuration. Other considerations include environmental performance (acceptable operational temperature and humidity ratings), third party certifications, and system interactions.
When multiple filters are employed in a system, their interactions can significantly impact overall performance. It is essential to analyze how these filters work together to avoid unintended resonances or reduced effectiveness. In some cases, redundant filtering stages can provide additional suppression and improve reliability, especially in critical applications. If a device already incorporates an internal EMC filter, adding an external filter requires careful consideration. The two filters must be compatible in terms of impedance and frequency response to avoid conflicts. Evaluating the combined performance of internal and external filters is necessary to ensure they complement each other and maintain system integrity.
Engineers often face difficult tradeoffs when selecting EMC filters. Balancing size and performance is a common challenge, as larger filters may offer better suppression but can be difficult to accommodate in compact designs. Similarly, there is a tradeoff between cost and effectiveness (as well as cost and regulatory acceptance), with high-performance filters typically coming at a higher price. Another consideration is the balance between insertion loss and bandwidth; while a high insertion loss provides better noise suppression, it may also attenuate desired signals, requiring a careful balance to maintain signal integrity.
RECENT TECHNILOGICAL ADVANCES IN EMI/EMC FILTERS – AMORPHOUS and NANOCRYSTALLINE CORE FILTERS
The evolution of core materials has played a pivotal role in enhancing performance and efficiency. Among these advancements, amorphous and nanocrystalline core filters have emerged offering distinct characteristics over traditional technologies.
Amorphous core filters are characterized by their use of amorphous metal, a material with a non-crystalline structure. Unlike the crystalline lattice found in conventional ferromagnetic materials, the amorphous structure of these metals lacks long-range order, resulting in unique magnetic properties. amorphous materials do not have this regularly repeating atomic arrangement. While there may be some short-range order, where atoms are arranged in a specific way over short distances, there is no repeating pattern that extends over longer distances. The lack of long-range order in amorphous materials is what gives amorphous core filters their unique advantages, such as high permeability and low core loss at high frequencies. Additionally, amorphous core filters are effective over a broad range of frequencies, making them versatile for various applications. Their high permeability and low loss also allow for a compact design, making them smaller and lighter than traditional counterparts without compromising performance.
Nanocrystalline soft magnetic materials offer a number of advantages: A higher permeability in the lower frequency band (tens of kHz) for better magnetic performance and damping, lower core losses to reduce heating and an improved thermal stability for operation over wider temperature ranges when compared to traditional ferrite materials. These core types are well suited for use in common mode inductors for EMC (Electromagnetic compatibility) filtering applications. The growing e-mobility industry, in particular the electric vehicle charging station sector is a target market for this material.
Traditional EMI filter cores are typically made from materials like silicon steel, ferrite, or powdered iron. Silicon steel, while cost-effective and widely used, suffers from high core losses at higher frequencies, making it less suitable for applications requiring efficient EMI suppression in this range. Ferrite cores offer good high-frequency performance but have lower saturation flux density compared to amorphous metals, which can limit their effectiveness in high-power applications. Powdered iron cores are versatile and provide good frequency response, but they typically have higher losses than amorphous cores at higher frequencies.
TDK-Lambda offers a wide range of EMI filters from DC input to AC input with single and three phase input for medical and industrial applications including high performance amorphous core filters. To find an EMI filter for your application visit our website at https://www.us.lambda.tdk.com/applications/emi-solutions/
Downloads
Power Guy
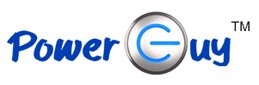