Power Supply Product Lifecycles and Designs for Industrial Equipment
Wednesday, February 14, 2024
Introduction
Receiving a component or product obsolescence notice is always an issue for any manufacturer of electrical or electronic equipment. Engineering time is diverted from new programs to find alternatives, then test and update product certification. Power supplies are often listed as a safety critical component and with offsite EMC testing, the overall cost can be between $25,000 to $50,000.
Low cost, high volume consumer products like mobile devices, usually have short product life cycles, driven by the need to satisfy a market demand for new features, faster processors and increased memory. It is rare that these types of products will be in production for more than one or two years. Legislation is frequently introduced to reduce off-load power losses and improve efficiency of the power supplies. This forces product redesigns and the obsolescence of a previous model.
A similar situation can arise in power supplies used in datacenters and similar high volume communication applications. Datacenters use very large amounts of electricity. The IEA (International Energy Agency) estimated the 2022 global datacenter electricity consumption was 240-340 TWh! Improving the efficiencies of the plug in, redundant AC-DC power supplies is one way of saving energy, often leading to short product lifecycles, as even a small reduction in power losses can reap large rewards. This too can result in early obsolescence.
Industrial equipment
Complex industrial equipment is very different. It will most likely be in production for five, ten or fifteen years, possibly longer, to meet the financial return on investment. The availability of replacement parts, like a power supply, to perform a repair even fifteen years later is expected.
Medical equipment requiring FDA approval have even longer product life requirements as obtaining FDA approval for a medical device is expensive and can take up to five years. Replacing safety critical parts due to an obsolescence notice is not a quick or easy task in that industry!
Industrial power supply design
The environment for industrial applications is usually harsher than that of a data center or data communication equipment which is typically in a temperature controlled clean environment. Industrial environments can have higher temperatures and are more likely to contain conductive dust or dirt which can cause power supply failures. The fans may be variable speed for longer life and to reduce the amount of contaminates being drawn in. The AC power may be subject to dips or surges from heavy equipment and switchgear, unlike a datacenter with filtered and back-up power.
Industrial power supplies tend to have heavier duty connectors to withstand vibration. They are built to operate continuously at full load rather than in an N+1 redundant system where the load is shared between two or more power supplies.
Finally, there will probably be multiple models in the series. The TDK-Lambda HFE series (Figure 1) of hot swap rack mount power supplies has two power levels, 1600W & 2500W with a choice of 12V, 24V, 32V and 48V outputs. The racks are available for screw terminal blocks on the input rather than IEC320 connectors and can be configured to deliver two different voltages within the same rack.
Figure 1: HFE industrial power supply and racking system
If the power supply has just one model on the datasheet and has a very attractive price, it is more likely to have been designed for a specific high volume application for one or two customers. If the production level drops there is a significant chance it will be obsoleted.
Please do not hesitate to call or email TDK-Lambda Americas Technical Support or your local sales office if you have any questions regarding a power supply for your next project. https://www.us.lambda.tdk.com/contact/
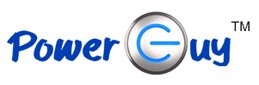