Why choose a power supply with a variable speed cooling fan?
Thursday, September 28, 2023
Introduction
A high power density power supply enables engineers to develop more compact products for industrial, medical and Test and Measurement applications. Most of these power supplies will require the use of forced air to remove internally generated waste heat, keeping it cool and operating reliably. That airflow can be provided by an internal fan or utilizing system airflow if available.
Forced air cooling disadvantages
Fan bearings
Fans require bearings which have a finite life. Most power supplies use ball bearings, rather than sleeve types as they are less prone to wear, can operate in higher temperatures and do not have orientation restrictions. The bearing life of a DC fan can be extended by reducing its speed and ensuring that cool air is drawn in across its bearings. In some analysis and microscope applications, the bearing vibration of the fan can impact the performance of the system.
Audible noise
As air is drawn through the fan, the blades create turbulence which generates audible noise. The amount of noise depends upon the speed of the fan, the fan guard, the design of the blades and the effect of that turbulence as it passes through the power supply. In many environments low fan noise is mandatory. For example, equipment in a hospital in close proximity to a recovering patient, or in test and analysis applications where long term operator exposure can cause fatigue and stress related injuries.
The lower the profile of a fan cooled power supply will likely result in a smaller diameter fan being used. A product that is 63.3mm high will use a 60 x 60mm fan, whereas a 40mm high (1U) will be restricted to a 40 x 40mm fan. To get the comparable airflow of a 60mm fan from a 40mm fan will necessitate in the fan being run faster, which will increase the amount of audible noise it generates.
Ingress of dirt and contaminants
Dirt and contaminants can be drawn into a system, particularly if the fan drawing in air is mounted close to the floor. Conductive particles can build up inside the power supply and cause premature product failures. (Figure 1).
Figure 1: Dirt build-up inside a power supply
A higher airflow speed will draw in more particles. These particles can be as small as the metalized dust from bank notes and coins! Air filters can minimize the ingress and some products like the GENESYS+™ programmable power supply series have an optional snap-on filter (Figure 2).
Figure 2: GENESYS+™ with air filter attached (top)
Using system airflow
The system fan (or fans) can be used to provide cooling to the power supply, often with less audible noise. A great deal of care must be taken to ensure that the power supply receives sufficient airflow at the right pressure. Often that air has to channelled directly to where the fan is normally mounted.
How do you know if there is sufficient cooling? The manufacturers application notes, instruction manual or safety files should provide guidance.
The best method is to place a power supply with the critical components thermocoupled in the end system to ensure they are all within rated temperature. For example, power supply electrolytics running too hot can severely reduce the field life. Some manufacturers will offer a unit with thermocouples attached (with recommended temperatures) to ensure the critical components can be tested in the end system.
Variable speed fans
One alternative to reducing the fan speed is to use a power supply with a variable speed fan. A temperature sensor will be mounted inside the product and a control circuit will increase the voltage to the DC fan if the temperature rises. Likewise, if the output load decreases, then the fan speed will be reduced along with the audible noise level.
The monitoring point may vary between manufacturer and product series.
For example, TDK-Lambda’s modular QM series (Figure 3) monitors the incoming ambient air temperature drawn in by the fan.
Figure 3: QM5 modular power supply
A modular power supply is constructed using modules to supply multiple output voltages. The ambient air maybe elevated at say 50oC, but the loading on the power supply may be minimal. This can result in a higher fan speed than is necessary to cool the power supply.
Monitoring the temperature at multiple locations
One way of keeping the fan speed as low as possible to reduce noise is to monitor the internal temperatures at multiple locations. Care has to be taken to ensure the primary to secondary isolation barriers are not compromised.
TDK-Lambda’s MU4 modular power supply is only 41mm high for 1U high applications. This of course restricts the fan size to 40mm x 40mm. As previously mentioned, a smaller diameter fan requires a higher rotation speed to generate a higher volume of air and would most likely result in a higher audible noise level.
To reduce the audible fan noise, the MU4 monitors the temperature at multiple locations. (Figure 4).
Figure 4: MU4 power supply and its thermal monitoring locations
An intelligent fan speed control circuit (patent pending) uses a microcontroller algorithm to monitor the temperature of the primary converter and each individual secondary module. This enables the speed of the fan to be accurately adjusted and optimized to provide an audible noise as low as 36dBA, even with an 80% load.
The output modules are automatically selected using TDK-Lambda’s on-line Quick Product Finder (click here). If a user requires a high load level from one particular output module (which may require the fan to increase speed), and a low level of noise is strongly desired, two modules can be used to halve the load level. The fan control circuit would sense the lower module temperatures and reduce the fan speed accordingly.
Always have a conversation with a power supply manufacturer at an early stage in your design. Their field application engineers or technical support staff may be able to give you insights into technology or products that will make your job easier!
Power Guy
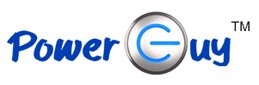