Using high voltage distributed power for large systems
Thursday, May 25, 2023
Multiple DC output voltages capable of supplying up to 45kW or higher of total power are frequently needed in many industrial applications. These can be found in semiconductor fabrication, large inkjet printers, test and burn-in systems. It can present a major challenge to engineers, not just on what power supply to use, but how to distribute large amounts of current and how to manage cooling. This blog will present methods of creating a viable high power source.
Input voltage
A power supply that can operate from a 400, 440 or 480Vac three phase input voltage will certainly be preferred because these are most prevalent in a factory environment. Using a large and heavy step-down transformer to lower the voltage down to 208 or 230Vac will be expensive and add substantially to the cost of freight. Many systems will be built in one location and shipped to another. The logistics are easier if, after final test, the equipment can be broken down into smaller, more manageable sub systems for reassembly on site.
Using multiple output power supplies
Multiple output AC-DC power supplies capable of operating from three phase are not that common and hence may be expensive (Figure 1). When loads are located a distance from the multiple output power supply, voltage drops over long output cables may be an issue even with remote sense compensating for the voltage drops. When the loading is transient in nature this may further compound the problem with oscillations caused by the cable inductance.
Figure 1: Block diagram of a multiple output power supply
Using single output power supplies
Using a number of single output power supplies may present other problems (Figure 2). The combined AC inrush current may be much higher. EMI issues may present a challenge as they will be operating at different switching frequencies and could cause a resonant beating effect.
Figure 2: Block diagram using single output power supplies
Using a low voltage DC bus
Another solution is to install one or multiple single output AC-DC power supplies, often in parallel to create a 48Vdc bus. 19” rack mount, hot-swap, current sharing products are frequently used in this application, like TDK-Lambda’s HFE series. 48V input isolated DC-DC converters are then used to provide locally regulated voltages next to the load (Figure 3).
For systems requiring higher power, this may present another challenge. A 10kW load will require 10,000W ÷ 48V = 208A. This may require the use of bulky, inflexible copper busbars to distribute the intermediate 48Vdc source to the individual DC-DC converters. Likewise, a 24V bus would require 416A.
Figure 3: 48V intermediate bus architecture using isolated DC-DC converters
Note that in this configuration there are two isolation barriers. One providing primary to secondary isolation and another lower voltage isolation in the DC-DC converters. This will allow the output of the converter to be used as a positive or negative output. A number of manufacturers offer 48V input DC-DC converters.
Using a 380V DC bus
More recently, driven by the use of 380Vdc in datacenters to reduce power losses and hence cut energy costs, designers are considering the use of a high voltage DC bus. Connectors, wiring and fuses capable of operating at the elevated voltage are now readily available. This type of design also simplifies the integration of renewable energy sources from solar, wind, hydrogen and energy storage battery technologies.
This type of configuration uses a non-isolated AC-DC power supply with the primary-secondary barrier in the DC-DC converters (Figure 4).
Figure 4: 380V bus architecture
DC-DC converters in this arrangement can operate from the 380V and typically have an input range of 200V to 425V. TDK-Lambda’s PH-A series (Figure 5) offers converters from 50W to 1200W in quarter, half and full brick packages with output voltages from 3 to 57.6V. The input to output isolation is 3,000Vac, input to baseplate 2,500Vac, and the output to ground 500Vac. All the modules are certified to the IEC 62368-1 safety standard and like the 48V bus system, the modules can be mounted close to the load.
With a 380Vdc bus, large bus bars are no longer needed to carry high amounts of current. Our previous 10kW load example would require wiring to distribute just 26.3A (10,000W ÷ 380V) rather than the 208A for a 48V bus.
Figure 5: PH1200A280 1200W DC-DC (full brick) converter
An example of a suitable AC-DC non-isolated power supply is the modular 4.5kW to 45kW rack mount TDK-Lambda TPF45000-385 (Figure 6). It has an extremely high efficiency of 98%, significantly reducing waste heat. The TPF can operate from 400/440/480Vac (Nominal) 3 Phase Delta or Wye input voltages.
Figure 6: TPF45000-385 non-isolated front end power supply
For smaller systems, the 1,500W board mount, baseplate cooled PF1500B-360 non isolated AC-DC converter can be used with up to three units in parallel.
Cooling the power system
In any large power system, waste heat management is a significant factor. Cooling heatsinks utilizing fans is possible but generates significant audible noise and can result in operator fatigue. Dust and other airborne contaminants may also be drawn into the system, impacting reliability.
Power modules like the PH-A series can be conduction cooled through their baseplates, allowing the use of liquid cooling, which is often already available in large test systems.
Summary
With a wide choice of power supplies on the market, it is highly recommended to partner with a power supply company that has experience with a broad range of applications. Their knowledgeable, locally based, Field Application Engineers can offer invaluable advice and interface between the user and the design teams. This can save time, money and speed up system compliance.
Power Guy
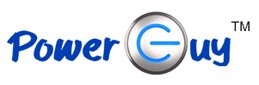