How to protect equipment operating from a 28Vdc vehicle source
Monday, February 27, 2023
What vehicles use a 28Vdc source?
Large trucks, buses, recreational vehicles (RVs), non-civilian vehicles and light aircraft use 24V rather than 12V batteries. 28V generators or alternators are used to charge them, hence the term 28V is used to describe the system voltage. Using a higher source voltage reduces the current drawn by system loads allowing smaller gauge copper wiring to be used. This in turn reduces weight.
Which standards apply?
That 28V input voltage does not remain perfectly regulated though. Automakers utilise ISO (International Organization for Standardization) standards ISO 16750-2 and ISO 7637-2 to ensure that any electrical or electronic assembly can withstand a wide range of input voltage variants without malfunctioning. These transients can be caused by incorrectly starting a vehicle using jumper cables for example.
Likewise, the US Department of Defense created MIL-STD-1275E. This standard covers the limits of transient voltage characteristics and steady state limits of the 28Vdc electric power circuits for military and vehicles. Depending on the application, sections of MIL-STD-461 may apply for low frequency conducted emissions.
For electronic equipment to pass testing and operate reliably, a transient filter may be required to avoid DC-DC converters and other components in the end systems being damaged. Two commonly used filter types are passive and active.
Passive filters
A passive filter is very simple (see Figure 1), using a combination of inductors and ceramic capacitors. It will suppress unwanted high frequency electronic noise from either impacting the performance of equipment or impacting other equipment using the same DC source.
Figure 1: TDK-Lambda FQA passive filter schematic
Figure 2: Typical FQA connection diagram
Figure 2 shows how the passive FQA filter is used with two HQA DC-DC converters. Com (in) is connected to system chassis ground and Com (out) to the 0V common (ground plane) of the converters. The capacitor shown with dotted lines can be placed between both modules Vin(+) and Vo(+) pins and between the Vo(-) and Vin(-) pins (4 places), further reducing high frequency common mode noise. This minimizes the chance of layout related compliance issues. As the capacitors cross the DC-DC converter’s isolation barrier, their voltage rating must be selected to meet the system isolation requirements.
Active Transient filters
These still use passive inductors and capacitor components to suppress the high frequency noise. They are used in conjunction with active circuitry to help protect the equipment against a variety of other faults or transients and offer the ability to electronically (inhibit) turn off the DC-DC converters or load.
Figure 3: TDK-Lambda FQB active filter schematic
Figure 3 shows protection circuitry in series with the passive filter components. A MOSFET provides reverse voltage protection which is kept in an off condition and will only conduct if the input polarity is correct. In the event of an under or overvoltage condition, the MOSFET is turned off until the input returns to within the correct operating parameters.
The protection circuitry also provides overcurrent protection. During an overcurrent event, the FQB module will limit the output current and initiate a timer. Once the timer reaches its threshold, it will shut off the internal power MOSFET switch to allow it to cool down and then attempt to auto-restart. The shut-down timing varies, becoming shorter as the severity of the fault increases.
The module features a soft start function to help avoid tripping the over-current protection feature while output load capacitors are charging.
The control circuitry enables the output of the filter to be turned off, either electronically or by using a switch. The circuit can also be used as a fault warning signal when connected to the DC-DC converter inhibit (remote on/off) terminals.
When the FQB Remote On/Off function is in an ON state and the FQB detects it is in a power good condition, it will enable the DC-DC converters. When an overcurrent or voltage fault occurs, the control function will turn off the converters and reduce any stress on the power system. The timing of the signal varies, becoming shorter as the severity of the fault increases.
Figure 4: Typical FQB connection diagram
In Figure 4 displays a typical connection diagram for an FQB filter and two HQA DC-DC converters. As with the active filter, the capacitor connected across the DC-DC input and output provides additional filtering . Filtering may be duplicated in four places on all the DC-DC converters positive and negative inputs and outputs.
Figure 5: TDK-Lambda FQB active filter (1/4 brick format)
Summary
If equipment being used off a 28Vdc source is expensive, requires a low emission environment or where high reliability is essential, consider adding an active or passive filter.
As a further benefit, many filters use baseplate cooling for removing waste heat and can be conduction cooled to a cold plate to avoid the use of cooling fans.
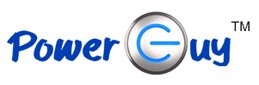