DC-DC converter switching frequencies – fixed or variable?
Monday, April 25, 2022
One power supply question our Technical Support team often get asked relates to the switching frequency. Usually this is to determine if it will interfere with a system’s clock or cause conducted and radiated emission issues.
DC-DC converters use high frequency conversion circuits to provide regulated DC outputs and input to output isolation where applicable. These frequencies are typically in the range of 50kHz to 500kHz. Depending upon the power supply topology these frequencies are either fixed or variable.
Recently, one of our fixed frequency DC-DC converters was selected to replace a variable frequency converter. This was for a trackside rail application for logistical monitoring of passing trains. A radio signal was being used to communicate between the trackside enclosure and the railcars. The variable switching frequency from the converter was causing communication problems.
After reading articles on the benefits of variable and fixed switching frequencies, I decided that this would be a good subject for a blog.
Pulse width modulation (PWM)
PWM is the most popular form of controlling the output of a power supply or converter. The frequency remains fixed, but the duty cycle changes to compensate for any changes in the input voltage, output voltage, or output load changes. (Figure 1).
Figure 1: PWM converter on and off times
PWM fixed frequency advantages
With a fixed frequency the switching noise is predictable.
The design is often simpler.
No audible noise at light loads.
If available on the converter, a frequency synchronization function (sync signal) can avoid beat frequencies by having multiple converters all operating at the same frequency.
PWM fixed frequency disadvantages
The fast rise and fall switching currents will generate high frequency, high energy noise at multiple harmonics. This may cause an increase in the size of the filtering.
On low power designs the switching losses at low loads can become predominant thus reducing the converter’s efficiency under light load conditions.
A high switching frequency can enable the use of a smaller transformer, inductor and filter capacitors. As the operating frequency is increased on a PWM converter, so do the switching losses.
To put the above in perspective, the TDK-Lambda i7A4W033A033V 500W 33A non-isolated step-down converter (Figure 2) has an input voltage range of 18 to 60Vdc and an output range of 3.3 to 24V. The switching frequency is 600kHz and the package size is 34 x 36.8 x 12.7mm.
Figure 2: TDK-Lambda i7A 500W 33A non-isolated DC-DC converter
The efficiency versus load curves (Figure 3) for a 24V output and a 28V input (blue curve) demonstrate a very reasonable flat efficiency of 97 to 98% above 6A loading.
Figure 3: i7A efficiency versus load curves
Pulse frequency modulation (PFM)
Two types of PFM converter operations are available. A fixed on time or a fixed off time. For a fixed on-time type (Figure 4) the off-time is variable.
With a light load the frequency decreases and the off time is increased (left side). For higher loads, the frequency increases (1/T(on+off)) and the off time is reduced (right side).
Figure 4: PFM converter on and off times
PFM variable frequency advantages
A quasi-resonant topology PFM has minimal high frequency switching edges on the converter currents as they resemble a rectified half-wave sinusoid. This creates fewer harmonics. This design will produce fewer EMI harmonics due to the sinusoidal switching currents.
On low power designs, the switching losses at low loads are reduced as the frequency is reduced.
PFM variable frequency disadvantages
With a variable frequency the switching noise is less predictable.
At light loads, if the frequency drops below 20kHz, the converter may create a slight audible noise.
The design is more complex.
There are power supply controllers that offer a hybrid solution, normally operating in pulse width modulation and reverting to pulse frequency modulation at light loads. Digital controllers offer a large amount of flexibility to designers too. Often enhancing a product design for an ultra-low off-load power consumption for example, may cause unwanted delays when the load is re-applied.
When considering which DC-DC converter to use I would recommend listing the specifications that are important to your system, in order of priority. Efficiency and off-load power consumption would be more important for battery powered equipment, size and weight for drone or robot applications. Fixed or variable operating frequencies may or may not even appear on the list until EMC testing is started; however, it is worth considering.
Power Guy
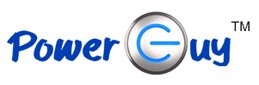